Manufacturing
Transform Your Manufacturing Operations with Gazer3D
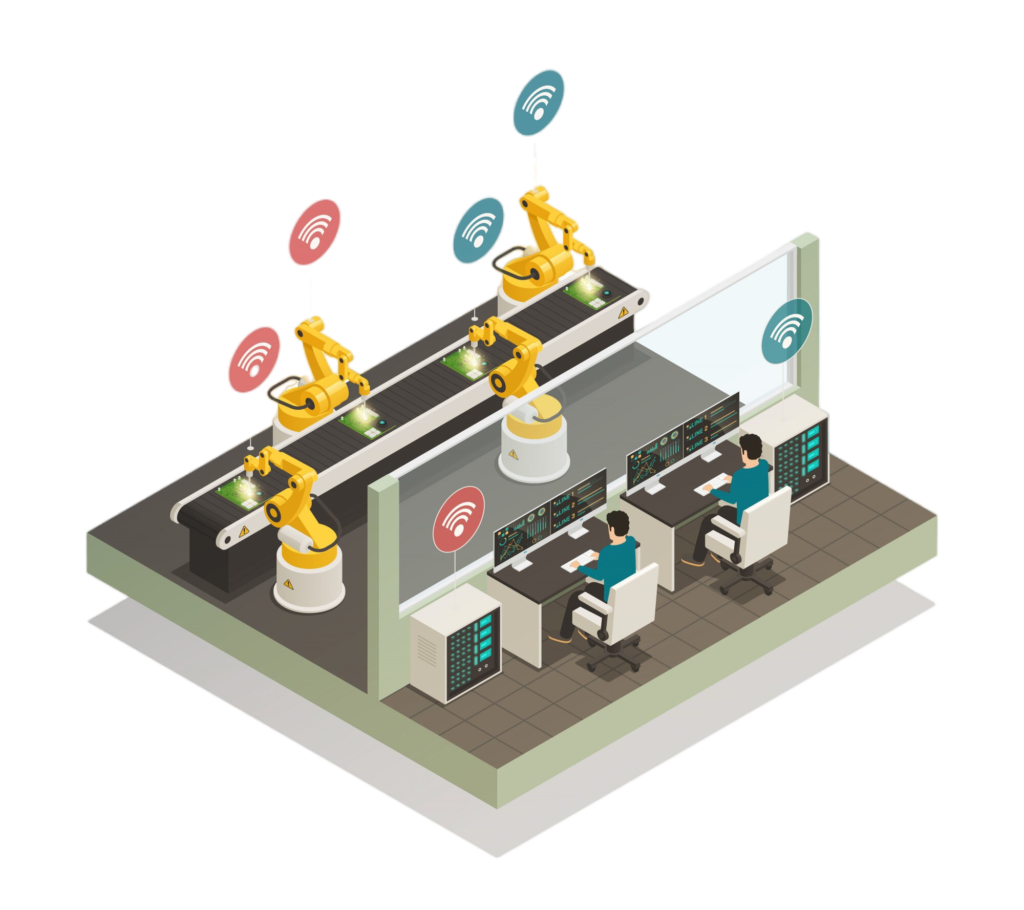
Introduction
The manufacturing industry is constantly evolving, with increasing pressure to enhance efficiency, reduce costs, and maintain high product quality. Gazer3D is at the forefront of this transformation, offering cutting-edge digital twin technology designed to streamline operations, optimise production processes, and drive innovation. Discover how Gazer3D can revolutionise your manufacturing workflows and set you on the path to Industry 4.0.
Key Benefits:
– Optimise Production Processes: Achieve seamless integration of real-time data and predictive analytics to fine-tune your production line.
– Enhance Product Quality: Use advanced simulations and modelling to improve product design and reduce defects.
– Reduce Downtime: Implement predictive maintenance strategies to foresee potential issues and minimise unplanned downtimes.
Industry Challenges
Manufacturers face numerous challenges, including managing complex production schedules, ensuring product quality, and minimising equipment downtime. The need for agile and efficient operations is more critical than ever to stay competitive in the global market.
Gazer3D Solutions
Gazer3D addresses these challenges by providing a comprehensive digital twin solution. It integrates with your existing systems to create a virtual replica of your manufacturing processes. This digital twin allows you to monitor real-time data, predict maintenance needs, and simulate production scenarios, leading to optimised workflows and improved decision-making.
Features and Capabilities
- Real-time Data Utilisation: Seamlessly integrate IoT data for continuous monitoring of equipment and production lines.
- Predictive Maintenance: Utilise AI-driven insights to predict equipment failures before they occur, reducing downtime and maintenance costs.
- Supports integration with leading MES, ERP, and IoT platforms.
- Scalable architecture to handle large datasets and complex simulations.
- Advanced Analytics: Leverage machine learning algorithms to optimise production schedules and improve resource allocation.
- Simulation and Modeling: Run complex simulations to test different production scenarios and identify the most efficient processes.
- High compatibility with various industrial protocols and standards.
- 3D Model Integration: Incorporate detailed 3D models of machinery and production environments for precise analysis and simulation.
Why Choose Us
Let us change the way you think about technology.
Seamlessly integrate IoT data for continuous monitoring of equipment and production lines.
Utilise AI-driven insights to predict equipment failures before they occur, reducing downtime and maintenance costs.
Incorporate detailed 3D models of machinery and production environments for precise analysis and simulation.
Seamlessly integrate IoT data for continuous monitoring of equipment and production lines.
Run complex simulations to test different production scenarios and identify the most efficient processes.
Dui gravida integer commodo cursus ante vehicula lobortis quam dis at tristique.
How it works
Gazer3D integrates with your existing MES, ERP, and IoT systems, collecting real-time data from various sources.
A virtual model of your production line is created, incorporating detailed 3D models and real-time data.
The digital twin continuously monitors operations, providing real-time insights and predictive analytics.
Run simulations to test different production scenarios and identify optimal processes.
Implement the optimised processes and continuously refine them based on feedback and new data.
Delivering IT solutions that enable you to work smarter.
Lorem ipsum dolor sit amet, consectetur adipiscing elit. Ut elit tellus, luctus nec ullamcorper mattis, pulvinar dapibus leo.
FAQ
Frequently Ask Questions.
Gazer3D is designed to seamlessly integrate with major MES, ERP, and IoT platforms, ensuring smooth data flow and minimal disruption to your current operations.
Gazer3D utilises real-time data from IoT sensors, historical maintenance records, and production data from MES and ERP systems to create accurate and functional digital twins.
Gazer3D uses advanced machine learning algorithms to analyse data and predict potential equipment failures. This allows you to perform maintenance proactively, reducing downtime and maintenance costs.
Yes, Gazer3D’s scalable architecture and advanced simulation capabilities are designed to handle complex and large-scale manufacturing environments.
Many of our clients have reported significant reductions in downtime, maintenance costs, and defect rates, leading to substantial cost savings and improved operational efficiency.